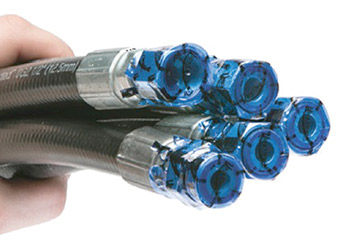
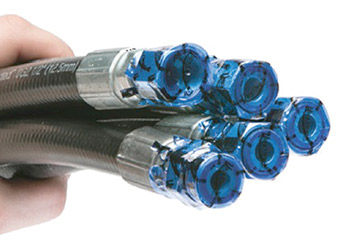
In the previous tech talks, MH Hydraulics FZC, a leading hydraulic solutions provider in the Middle East, focused on oil contamination. In the September, October and November 2020 issues, we recognised the importance of clean hydraulic oil and ways to prevent oil contamination. In the December edition, we discussed hydraulic hose safety and the importance of making the hose assemblies right the first time to avoid hydraulic oil contamination and downtime.
In this article, we explain the importance of hose storage, testing, cleaning, and packaging. An improperly cleaned and sealed hydraulic hose would cause oil contamination as soon as the hose assembly is put in the hydraulic system.
![]() |
|
Proper storage will maximise hose shelf life.
I. Store hoses in a cool and dry area. The ideal storage temperature is 15 deg C and the acceptable range is between 0 deg C and 35 deg C. In any case, stored hoses should not be subjected to temperatures in excess of 50 deg C or lower than -30 deg C.
II. Care should be taken when stacking hoses, as its weight can crush hoses at the bottom of the stack.
III. Avoid exposure to direct sunlight, rain, heaters and proximity to electrical equipment.
Hose assemblies should be tested for acceptable proof and burst pressure. It is recommended that proof and burst testing be performed in accordance with SAE J517 and SAE J343 — or an acceptable industry standard, or as per customer specification.
I. Proof pressure test: This test is to be conducted at two times the working pressure of the hose unless otherwise specified by the customer. Test pressure for not less than 30 seconds and not more than 60 seconds. There should be no indication of leakage or failure.
II. Burst test: Hydrostatic pressure test increased at a constant rate to attain minimum burst pressure for a duration not less than 15 seconds and not more than 30 seconds. There shall be no hose burst, leakage, or indication of hose failure below specified minimum burst pressure.
![]() |
|
RECOMMENDED HOSE CLEANING PROCEDURES
There are things you can do to make your cleaning process more effective. Following are three easy steps to improve your clean hose assembly process:
1. Do you really need that chop saw: When assembling a hydraulic hose, the very first step is to cut it to the correct length.
Obviously, this step is necessary, but it is also the biggest contributor of contamination to your new hydraulic line. Abrasive wheeled chop saws are the worst offenders. Try switching to a metal blade whenever possible to reduce the amount of debris generated by the cutting process, MH Hydraulics can help you select the right solution.
• Take it a step further: Try implementing a “clean cut” saw or blade that is specifically designed to minimise the ingress of contamination. MH promotes Finn-power.
2. Use clean air: Firing a projectile with dirty air is like mopping a floor with muddy water. It simply defeats the purpose. Wet air is even worse. Water particles will adhere to the walls on the inside of hose or tubing, capturing and retaining airborne dust particles and polluting the hydraulic oil on the equipment.
Using clean, dry air is one of the best ways to avoid recontamination. We recommend installing a 5-micron filter at the point-of-use to reduce contamination.
• Take it a step further: Implementing a compressed air dryer will eliminate the most common headaches by absorbing oils and water and filtering out solid air particles.
![]() |
|
3. Sweep your workshop: Keeping your workshop clean seems almost too mundane to mention but you’d be surprised at how few people give it any thought. All that grime gets kicked up and circulates around your shop, settling all over the place. It’s what we warn about when we mention “airborne particles”. It’s also the same air that will settle into your new hydraulic lines if not cleaned and capped correctly.
• Take it a step further: Try using a vacuum instead of a broom to avoid stirring up the dirt.
It’s important to note that putting these tips into practice is not a substitute for an effective cleaning process like the Ultra Clean System. These tips are a supplement for giving your system an edge, not a replacement procedure. In fact, ISO cleanliness tests show that only giving your hydraulic lines an air-blow – even with clean air! – doesn’t provide you any significant advantages.
![]() |
hose after cleaning with Ultraclean projectile |
NOTE: When a hydraulic hose is cut with metal-blade saws or abrasive wheels, tremendous heat is generated, causing rubber and metal particle and dust contaminants to stick to the hose or tube as they cool. It is vitally important to clean the hose immediately after the cutting process to avoid this. Fire one projectile in each direction through the length of the hose prior to installation of end connections. This will allow cleaning in the areas occupied by the insertion of the hose nozzle at either end. After crimping or swaging fittings, an Ultra Clean projectile should be fired through the entire hose assembly to remove metal flash. It is vital to apply clean seal capsules to hose ends immediately after cleaning to avoid recontamination, and to protect hose threads. The projectile strips out the internal contamination, removing dirt, gunk, and oil. Now, your clean oil will stay clean as it reaches those expensive components, preventing failure and system downtime. Ultra Clean Technology is one reliable supplier for hose cleaning and sealing solutions.
![]() |
|
CLOSE THE HOSE ASSEMBLY THE RIGHT WAY.
Once the hose assembly is made, it is important to seal the end fittings before delivery to the site for installation. There are clean seal system heat-shrink (a clean seal capsule tightly sealed around hose assembly fittings). These capsules can be used to seal one or multiple assemblies and is an advanced solution for keeping oil in your system and dirt out whenever you must disconnect or change a hose with flanged connections.
It’s important to note that putting these tips into practice is not a substitute for an effective cleaning process like the Ultra Clean System. These tips are a supplement for giving your system an edge- not a replacement procedure. In fact, ISO cleanliness tests show that only giving your hydraulic lines an air-blow – even with clean air! – doesn’t provide you any significant advantages.
![]() |
projectile with dirt after cleaning |
To conclude, following proper storage conditions improves the lifetime of hose assemblies:
1) Check the date on your hoses.
2) Follow the clean hose assembly procedures.
3) Do not use plastic closure plugs.
4) Demand a test certificate of the hose assemblies.
The above recommendations will provide you with a reliable hose assembly that is clean and safe.
MH Hydraulics is glad to assist you and will help you prevent unplanned down time of your equipment.
* This article is provided by MH Hydraulics
![]() |
|
![]() |
|
![]() |
|