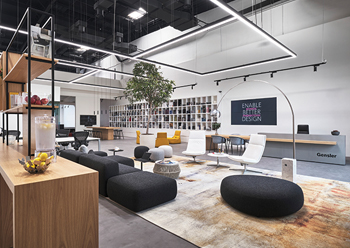
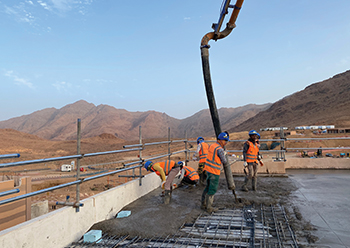
Al Kifah Ready-mix and Blocks (KRB), a veteran in the concrete products sector in Saudi Arabia with a 40-year legacy behind it, is leading from the front in its drive towards greener construction. Having launched its “green concrete” – ConGreen – last year, the Eastern Province-headquartered firm is now set to launch operations of a natural pozzolan plant.
ConGreen boasts a number of sustainable and environmental benefits, whilst providing high durability, improved performance, and better workability and pumpability properties. ConGreen concretes replace cement with lower-carbon materials such as pozzolan and use Canada-based Carbon Cure Technologies’ embedded recycled carbon dioxide (CO₂) technology to reduce its carbon footprint by up to 30 per cent compared to conventional ordinary Portland cement (OPC) concretes, according to KRB.
Al Kifah Ready-mix and Blocks currently offers nine types of ConGreen for applications ranging from non-structural to decorative, heavy-strength and underwater.
In line with efforts to reduce emissions in the production of all four key components of concrete – namely cement, aggregate, admixtures and water, KRB is now poised to bring its natural pozzolan plant on stream in the second half of this year.
“Natural Pozzolan (NP) can be used to replace cement by up to 30 per cent,” says Ahmed F Taha, R&D/Technical Manager at Al Kifah Ready-mix and Blocks.
“Recently, there has been increased attention given to research on local natural pozzolan due to the increase in cost of imported supplementary cementing materials (SCMs) and high carbon dioxide emission attributed to their transportation.
“Intensive research studies conducted at Alkifah’s R&D Centre have proved the good performance of local natural pozzolan,” he adds.
According to Al Kifah, the Natural Pozzolan plant is in the final engineering phase.
KRB revealed these details during a presentation entitled “Net Zero Carbon Concrete in Saudi Arabia – RoadMap – Opportunities – Challenges” at The Big 5 Saudi held in Riyadh from February 18 to 21.
![]() |
ConGreen-N is suitable for all types of substructures/superstructures. |
KRB pointed out that the construction industry is responsible for the emission of a large amount of carbon dioxide into the atmosphere annually, accounting for about 11 per cent of the total global emissions. In concrete construction, all four components of this basic material release CO₂ into the atmosphere both through direct emissions (manufacturing and fuel consumption) and indirect emissions (electricity used for external production, transportation of inputs and outputs, products bought from third parties, etc).
“In normal practice, a concrete mix can be roughly estimated to consist of 10-22 per cent of cement, six to eight per cent of water, 26-38 per cent of fine aggregate and 38-48 per cent of coarse aggregate. However, cement accounts for the highest CO₂ emission per unit-weight among all components. Therefore, in order to reduce the amount of CO₂ emission in any concrete mixture, it is quite clear that cement should be the main target,” Taha said.
For each ton of Ordinary Portland Cement (OPC), 0.7-1 ton of CO₂ is emitted. As much as 50 per cent of these emissions come from the manufacturing process, 40 per cent come from the energy combustion required to heat that process; and 10 from other sources, he added.
The solution is to decarbonise cement by replacing clinker with pozzolans, using alternative fuels, ensuring energy efficiency and adopting emerging CO₂ utilisation technologies.
Some of the measures that can be adopted is reducing clinker volume by increasing the volume of decarbonated raw materials particularly those that can be sourced locally and are not transported over long distances to replace some of the clinker in the kiln.
“Some of the initiatives being taken in Saudi Arabia is the use of Pozzolan Portland Cement (PPC) which complies with SASO-ASTIVI C595. It is currently being produced by five companies in the Western and Northern provinces of the kingdom. Here, about 30 per cent of clinker is replaced by local pozzolanic material,” he said.
Energy efficiency can be boosted by implementing electrical retrofits and improving milling operations, such as by switching from ball mill, which is energy intensive, to vertical roller mill grinders.
According to Taha, carbon capture, utilisation and storage (CCUS) technologies play a key mitigation role in the decarbonisation of cement and concrete. The captured CO₂ can be reused in the concrete industry through different technologies such as CarbonCure Technology and Carbonation Curing Technology.
“CarbonCure injects CO₂ into readymix where it converts to a mineral – solid limestone or calcium carbonate (CaCO3) – improving the material’s compressive strength by 10 per cent. This allows to optimise mix designs and safely reduce cement content by up to five per cent, thus lowering the carbon footprint of concrete, with no impact on quality or performance. The technology enables the carbon footprint of concrete to be reduced by about 15-20 kg/cu m of concrete. CarbonCure complies with ASTM C494 Type S,” he says. The sequestration of CO₂ is monitored by CarbonCure and verified by a leading independent body, VERRA, thus enabling generation of carbon credits traceable on the international markets.
Carbonation curing, meanwhile, is an accelerated curing process that must be carried out within 24 hours after casting. If done immediately after casting, it results in a significant increase in early strength of concrete.
“In a study conducted jointly by Alkifah and Aramco, it was found that time taken to demould after the curing of concrete was reduced by more than half, from 18 hours to just eight hours,” he added.
Also, the durability of concrete was enhanced by 15 to 35 per cent. The study concluded that using these technologies, 1 mtpa of CO₂ can be sequestrated by the precast industry in Saudi Arabia.
The traditionally used SCMs are fly ash ASTM C618 that can replace up to 35 per cent of cement as per ACI 211; ground granulated blast furnace slag (GGBFS) ASTM C989, which can replace up to 70 per cent of cement as per ACU 211; and silica fume ASTM C1240, which can replace up to 15 per cent of cement as per ACI 211. Recently, research into innovative SCMs such as local natural pozzolan has gained interest due to the increase in cost of imported SCMs and high CO₂ emission attributed to their transportation, he said.
Another material that is gaining attention is geopolymer, which comprises aluminosilicate-rich materials and alkali, which is being used in building construction, infrastructure and industrial construction, among other applications.
Aggregates emissions
There are three main sources of CO₂ emissions in the production process of coarse aggregates: production and transport emissions; electricity consumption; and from purchased goods and services. One solution to address this issue is using recycled aggregates. Two kinds of recycled aggregates have been tested by Alkifah R&D centre and are currently available commercially in various sizes in the Saudi market, namely: Metal slag aggregates (MSA), manufactured from iron and steel slag; and recycled aggregates from construction demolition wastes (RADW).
ConGreen
KRB, which has grown steadily since 1980 to enfold more than 27 branches all over the kingdom, currently offers nine types of ConGreen:
• ConGreen-HS, marketed under the brand Tuwaiq Crete: a high-strength concrete with a low CO₂ emission factor and low heat of hydration. Boasting a compressive strength of 50 to 80 Mpa or higher, it is designed for structures that need high-strength, such as high-rise structures and bridges;
• ConGreen-SC (Sail Crete), a flow concrete characterised by self-consolidating, high pumpability in addition to having a very low CO₂ footprint. With a compressive strength of 28 to 80 Mpa, it is suitable for structures that need self-consolidating concrete, such as bridge decks, tunnel lining, tubing segments or structures with a high rebar concentration;
• ConGreen-UW (Lulu Crete), a concrete characterised by high cohesiveness and rheology in underwater environment, with a compressive strength of 20 to 50 Mpa;
• ConGreen-HT (Jelmood Crete), a heavyweight concrete made with heavyweight aggregates and Pozzolan materials in addition to using low CO₂ emission technologies in its production. With a strength ranging from 30 to 60 Mpa, it is designed for radiation shield structures, counterweights and other applications where higher density is desired;
• ConGreen-Spray (Qara Crete), a high-performance shotcrete (sprayed concrete) suitable for curved structures (including shell roofs and domes and tunnel linings) and free-formed structures (such as swimming pools and climbing walls) and others. It has a compressive strength of 25-40 Mpa;
• ConGreen-N is suitable for all types of substructures/superstructures with a strength range of between 17 and 40 Mpa. It has a very low CO₂ emission factor and high workability;
• ConGreen-C, a coloured concrete for special architecture and infrastructure applications with different strength grades as per project specifications. All strength grades are available.
• ConGreen-LT, a lightweight concrete with densities range 800-1,900 kg/cu m designed for use on different structures with a specified density concrete, such as bridge decks, parking structures, tilt-up walls, etc. It is available for nonstructural (2-16 Mpa) and structural applications (17-35 Mpa); and
• ConGreen-M, a mass concrete with very low heat of hydration for large structures such as dams, bridge piers, and other large volume placements, with a strength range of 30 to 60 Mpa.