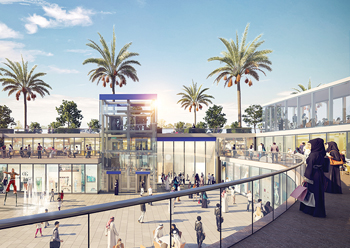
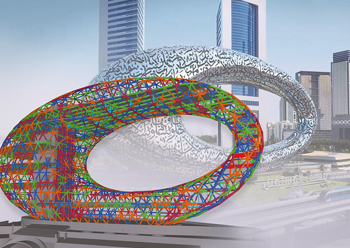
After a prolonged slowdown, especially in the GCC construction industry, triggered by the crash in oil prices and further deepened by the impact of Covid-19, the sector is showing a promise of recovery. Despite the headwinds, there’s an indication that 2022 will see a stronger pipeline of construction and transport infrastructure projects, and the GCC region is expectedly looking towards a new era of development in the near to mid term. Thanks to digitalisation, construction companies can now address major issues such as project delays and onsite safety with much more ease and confidence than ever before and, with a technology-enabled framework, are able to deliver complex projects with more precision and efficiency.
Despite the availability of modern technologies to connect stakeholders, workflows, and project data, the various teams and processes involved in project building often remain separated and tend to work in silos. Engineers lack the details needed to produce more constructible models and contractors have to make do with the virtual models with limited information, accepting that changes on the construction site are a part of the process.
However, these changes turn out to be costly for the project in terms of duplicated efforts, rework, and waste, unnecessary arguments between contractors, engineers and business owners, creating a ripple effect of inefficiency, ultimately resulting in the budget and schedule overruns that hurt the construction industry.
![]() |
Wallett ... aiming for a dynamic, always-up-to-date BIM model. |
Digital as-builts
More collaboration among construction stakeholders is required to develop infrastructure assets efficiently and sustainably, and project data must be centralised and accessible to all teams. This can be accomplished with the help of a collaboration tool that connects the right people to the right data at the right time, allowing more informed decision-making and increased project productivity.
This is where digital as-builts come into play, which necessitates all stakeholders sharing a single, centralised 3D model where data is captured throughout the construction process. The outcome is a dynamic, always-up-to-date BIM (building information modelling) model that goes beyond design to help with planning and decision-making during and after construction.
The digital as-built model can also serve as the foundation for a digital twin, a live model of the asset that can be used to diagnose and predict defects, run simulations, and evaluate the asset’s status in the context of its surroundings and usage once it’s in use.
A potent digital as-built allows owners to access the granular data as well. Also, engineers can design a higher level of detail and develop better constructible models. Potential faults can be recognised and rectified prior to costly rework or RFIs, thus leading to faster delivery, cheaper costs, and better transparency throughout the project.
![]() |
A Riyadh Metro station ... advanced 3D modelling tools have been utilised. |
Implications for various stakeholders
Engineers have a better control on the owner’s expectations from the outset, since digital as-builts require owners to precisely communicate the type of information they want to see in the as-built model. They can also engage with contractors earlier in the process by using the shared model. Proactive firms can collaborate to discover and address design concerns before they reach the field, saving owners money and giving themselves a competitive advantage.
On the other hand, contractors can start with a constructible model for actual construction. The changes can be documented in the common 3D model, obviating the need for manual and redundant work. For the network of vendors that contractors work with, the virtual model becomes a single source of information. The model’s data can subsequently be used to regulate machines used for construction work, resulting in increased productivity and sustainability by decreasing waste.
The data-rich approach also allows for the deployment of augmented and mixed reality technology as more teams operate remotely, allowing them to collaborate and interact with the jobsite from anywhere. Contractors can also use extended reality tools to better train personnel and help them visualise and avoid site safety hazards.
Further, data-rich digital as-builts enable owners to make better informed decisions, besides managing operations and maintenance. Or they can use the digital as-built to diagnose the cause of an issue by accessing history about how the asset was built, the materials used, the conditions during construction, and more.
Connected Construction
However, to realise the many benefits of digital as-builts, a cultural shift is required on how the construction projects should be managed, from the way they are traditionally managed. To enable that shift, stakeholders need an underlying technology framework that facilitates the sharing of information, while enabling connectivity between specialised tools and systems used throughout the construction lifecycle, from design through post-construction. This is where Trimble Connected Construction comes in. From concept to onsite operations, this software solution connects each lifecycle phase of civil construction projects. By providing the framework needed to improve data sharing and communication among the various stakeholders, Connected Construction is the underpinning that weaves the people, processes, and technology together.
Today, the infrastructure sector in the Middle East and North Africa (Mena) region is booming and there is no shortage of potential project opportunities waiting to be unlocked. Digital as-builts have the potential to provide additional transparency and problem-solving opportunities. Engineers will have better insight into potential issues and risks that may happen along the way and come up with solutions to prevent any untoward results from occurring. Now is the time that stakeholders across the infrastructure ecosystem to explore the opportunities that lie within digitalisation as infrastructure investment ramps up, and maximise project efficiency and profitability.