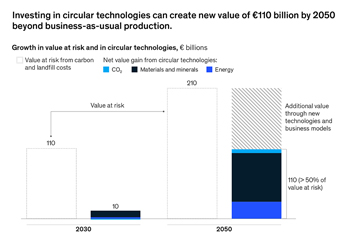
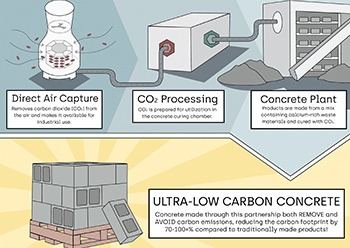
The world’s first on-site, fully-integrated Direct Air Capture (DAC)-to-concrete commercial production facility is currently being built in the US, leveraging technology from three key stake holders in the concrete production section.
The 4 Corners Carbon Coalition, a network of US local governments committed to addressing the climate crisis with carbon removal, has awarded $150,000 to develop the facility, which will be developed by CarbonBuilt, an ultra-low carbon concrete technology developer, Aircapture, a modular DAC technology developer, and Block-Lite, a concrete products manufacturer.
The process is expected to reduce the embodied carbon of the resulting concrete blocks by more than 70 per cent compared to traditional concrete.
How it works
CarbonBuilt will install its patented and XPrize-winning technology on-site at Block-Lite. Its technology dramatically reduces the use of cement in concrete products by replacing it with a proprietary mix of low-cost and low-carbon industrial waste materials that are sourced locally. It then uses CO₂ to cure the mix into concrete blocks. Critically, the blocks can be sold at price parity, and are compliant with ASTM C90 and other relevant standards.
Aircapture’s modular DAC technology reliably supplies commercial and industrial customers with clean CO₂ captured from air onsite, when and where needed. The company will build an array of DAC units, each designed to capture approximately 100 tonnes of CO₂ per year. The CO₂ will be routed into CarbonBuilt’s gas processing system to be conditioned before being mineralised and stored permanently as concrete.
CarbonBuilt and Aircapture technologies will be installed at the Block-Lite manufacturing facility, a third generation, family-owned and operated business in Flagstaff, Arizona. The addition of DAC follows a years-long commitment to decarbonisation by Block-Lite, which already has installed a large-scale solar array on-site to power its operations.
Environmental Impact
This combination of CO₂ avoidance (by reducing cement use) plus CO₂ removal (via mineralisation) can result in concrete that reduces embodied carbon by more than 70 per cent compared to traditional concrete.
Collectively, the project is expected to avoid 2,000 to 3,000 tonnes of CO₂ emissions plus remove more than 500 tonnes of atmospheric CO₂ per year per production line.
New Model for DAC
This project represents a new model for DAC in several ways. First, atmospheric carbon is not just buried, but treated as a valuable ingredient in a high-volume commercial product. Second, the on-site integration means no cost, complexity or human impact of CO₂ transportation. Last, because the technology is integrated at an existing manufacturing plant, there is zero land use impact. Block-Lite and CarbonBuilt become the “anchor tenants” for Aircapture, which intends to establish a broader local market for captured CO₂.
“Large-scale, durable carbon utilisation can play a critical role in driving down the cost of DAC and accelerating atmospheric carbon removal. The concrete industry’s scale and global reach uniquely position it as an enabling partner to the DAC industry,” said Rahul Shendure, CEO of CarbonBuilt. “We intend for this project to become a blueprint that can be replicated at many of the thousands of concrete manufacturing plants around the world. The grant from Four Corners is a key first step in the overall project plan and we look forward to building on the momentum with our partners.”
Matt Atwood, CEO of Aircapture, comments: “Atmospheric carbon dioxide removal and carbon utilisation into products is on the critical path to addressing climate change. While the common assumption of industrial carbon application is that of a short-lived product, we are demonstrating a novel solution to create permanent carbon storage sinks in our built environment. This exemplary project couples industrial decarbonisation together with cost savings, carbon removal, job creation and environmental co-benefits.”
“All too often sustainable building materials require a trade-off between cost and performance, but what is unique about this project is that there’s no ‘green premium.’ We’re going to be able to produce on-spec, ultra-low carbon blocks at price parity with traditional block which should speed adoption and impact,” says a spokesman for Block-Lite.