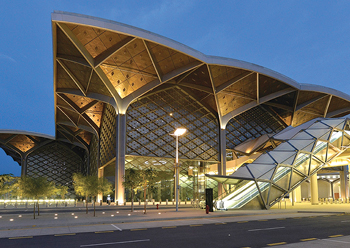
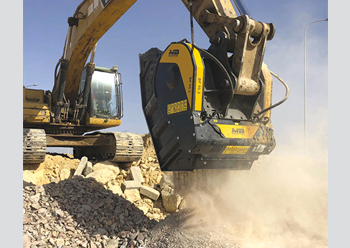
Italy-based MB Crusher, which for the past two decades has been offering the largest line of patented crusher buckets and accessories for excavators, skid loaders and backhoes, will be participating at The Big 5 Heavy and Middle East Concrete this month in Dubai.
“The Big 5 Heavy and Middle East Concrete events are dedicated to the infrastructure and concrete construction community, and we are participating to do our bit for the industry. We will display our units and also have a consultant at the stand OS 800 – outdoor to assist you,” says a spokesman for MB.
MB’s attachments can be installed on any brand of heavy equipment including midi excavators, loaders and skids. There is no need for modification of the machine, just simply plug-and-work, he adds.
Among the products promoted at the event will be MB’s jaw crusher buckets, screeners and a drum cutters, and on display will be BF90.3 crusher bucket, MB-S18 screening bucket and MB-R900 drum cutter. These attachments minimise procurement costs; save time by processing material on the spot; and save money by avoiding landfill and transportation costs, the spokesman says.
MB’s tools can help address the issues of managing materials from construction and demolition cost-effectively, while also tackling the challenges of supply shortage.
“Prices also change from month to month, becoming unsustainable for companies already struggling to meet all of their orders,” the spokesman points out.
To tackle this problem, one contractor handling demolitions purchased MB’s BF70.2 crusher bucket.
A spokesman for the company comments: “When dealing with demolitions, we have a lot of rubble to dispose of on-site – reinforced concrete, bricks, tiles, reinforced poles, etc – so we asked ourselves, ‘why not process this rubble directly on-site and reuse them?’ Above all, how do you successfully carry out this process?”
So, how did the company give waste materials a second life? Using a BF70.2 crusher bucket to reduce the material’s size, along with an MB-S18 screening bucket, the company cleaned and sorted the material on-site. With two attachments and one excavator, they produced quality material themselves, all ready to be reused.
“With MB Crusher’s equipment, the rubble becomes a resource capable of keeping the construction site active – even on locations where there aren’t materials readily available, or in areas with difficult access, or within cities while managing restrictions and being watchful of noise and dust emissions. The whole process takes place on-site and transforms waste into excellent recycled material. A practical and economically advantageous method that saves time and money; eliminate disposal fees and the cost of purchasing new materials. Once “cleaned”, the rubble can be reused for other jobs,” the spokesman says.
One useful tool in the process of recovering demolition materials is the MB Crusher sorting grapples. The winning feature of these grapples is the unit’s grip sensitivity: it allows extreme precision and progressively increases the closing force. Thanks to the interchangeable claws and the 360-degree hydraulic rotation, they managed larger loads and odd shapes, even in confined spaces, he adds.