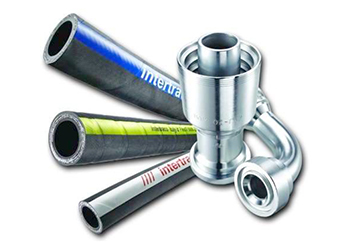
In the previous tech talks, MH Hydraulics FZC, a leading hydraulic solutions provider in the Middle East, focused on oil contamination. In the September, October and November 2020, it highlighted the importance of clean hydraulic oil and the ways to prevent oil contamination.
In this article, the company explains the importance of choosing the right hose for your application. A properly selected hose assembly will avoid early failure of the system and reduces the chances of oil getting contaminated as dirt particles can enter the system during the hose assembly replacement.
A hydraulic system’s hose assembly design needs to focus on the required working pressure, flow rate, medium, temperature and the application.
![]() |
|
1) Misapplication: Perhaps the greatest cause of failure is using a hose, fitting or clamp in an application that it is not designed for;
2) Kinking at or near the fittings: Once the barb of the fitting cuts into the tube of the hose, the product being conveyed can escape into the reinforcement and eventually lead to bubbling or blistering of the cover within several feet of the end;
3) Temperature exposure: As temperature increases, pressure ratings decrease. Excessive hot or cold temperatures will lead to discolouration, cracking, or hardness, as well the buildup of static electricity if the hose wire has not been ground properly;
4) Surging or excessive working pressure: Usually a large burst with torn reinforcement, typically along the outside of a bend;
![]() |
|
5) External damage to hose carcass: Kinks, crushed sections, and cover damage which expose reinforcement will eventually break down the reinforcement and lead to a hose failure;
6) Exceeding the minimum bend radius: Kinking, crushing, or forcing a hose to bend beyond its minimum bend radius (measured from the inside edge of the hose, not the centreline). This is commonly seen on high pressure hoses or vacuum hoses;
7) Defective hose or improperly installed or selected clamp: Failure from a defective hose will typically occur in the first few hours of service, such as pin holes, blow-outs, or tube and cover separation. Improperly installed or selected clamps can result in the coupling ejecting from the end of the hose. Always confirm the manufacturer recommendations based on stamped information;
![]() |
|
8) Tube or cover not compatible with fluids or environment: Usually results in discolouration, swelling, sponginess, or the breakdown of the hose carcass. For material handling hoses, always rotate to ensure even wear of the hose tube;
9) Old age: Hose is not a ‘pipe’; it is a flexible component that will degrade over time. Shelf or service life will range from 1 to over 20 years, depending on its composition, application, and environment. Older hoses become discoloured, stiff, or burst at low pressures;
10) Incorrect hose length: Too short of a length does not allow the hose to expand/contract due to changes in pressure or temperature and causes excessive stress on the fittings or hose reinforcement;
11) Twisting hose during installation or service: Twisting a hose rather than naturally bending the hose will reduce life. It is estimated a 7 per cent twist when installing a hose in a permanent application can reduce hose life by 90 per cent;
![]() |
|
12) Poor workmanship: Hose and fittings are made of a unique blend of different materials with complex manufacturing methods. Human error, inconsistent machinery, or poor product quality or raw materials can result in defects or variances greater than allowable tolerances. As for failure at the end fitting, ends blowing off assemblies can be a result of substandard coupling procedures or due to the “mixing-and-matching” of incompatible hose, couplings, or clamps.
There are various types of hose configurations available, such as wire braided hoses (that too with single wire), double wire, 4 wire, etc depending on the application. The manufacturer’s data sheets and guidelines are to be followed for selecting the right hose.
![]() |
|
For example, the picture shows a single wire braided hose where the first inner layer is synthetic wire tube, the intermediate layer is of high tensile steel wire braid, and the outer cover is of synthetic rubber. These are used for hydraulic oils, both mineral and biological; Polyglycol base oils, water/oil emulsions and water at temperature ranges 40 deg C to over 100 deg C.
Many other types are available such as textile braided hoses, helical and spiral wire hoses, stainless steel corrugated hose, etc. and should be selected depending on the application. Proper selection is key to a safe house assembly. The below shown chart is an example from Intertraco, a reliable supplier of hoses and fittings from Italy.
Several factors are to be considered while selecting the hose fitting, including the compatibility of the fitting to the hose, one- or two-piece design and the correct assembly.
It is highly recommended to use a one-piece hose fitting if possible. This is to avoid selection mistakes.
One-piece hose fittings have a ferrule nipple that is built with the hose fitting. Many try to re-use the existing nipple when replacing hose fittings. This is extremely unsafe. Always use new components to assemble or repair hoses.
![]() |
|
For hydraulic applications with extreme duty, skive hose assemblies are an option.
Never cut a hose with an abrasive cutting disk; always use metal cutting blade. This is to avoid contamination. Improper cutting tools give a chance for rubber, metal and abrasive particles to enter the hose and will create oil contamination when put into operation.
The correct equipment to use for hose crimping is extremely important. Finn-power from Finland has many years of experience to create a reliable crimp.
The cleaning of hose using foam pigs wherever possible and the use of shrink plugs while delivering ensure no dust or particles are inside the hose. Hoses, which are subjected to external abrasion, can be protected with external sleeves like that from Safeplast, in Finland.
For hydraulic hose reliability and minimising hose stresses, it is important to adhere to the correct routing of hoses.
To conclude, hose assemblies are integral part of any hydraulic systems. Utmost care must be done in the selection, manufacturing and its installation. The selection of hose fittings must be done based on the design parameters. Recommended operations and methods are to be followed to build a reliable hose assembly. Installation techniques are to be followed.
In our TechTalk #5, we will explain hose storage, hose testing and reliable/clean hose packaging. By being aware of the above, a safe, leak proof, long life hydraulic system can be achieved.
![]() |
|
Remember, one of the main causes of oil contamination is hose failure; oil gets contaminated during the process of replacing damaged hoses and fittings. Hence making hose assemblies the first time right, saves time, money and unplanned equipment downtime.
![]() |
|
* This article is provided by MH Hydraulics