 sml.jpg)
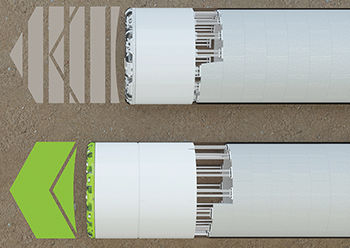
Herrenknecht says it has developed a new continuous tunnelling system for use in all common soft ground formations (with and without water-bearing layers).
The Germany based manufacturer claims to be the only company worldwide to deliver tunnel boring machines for all geologies and in all diameters – ranging from 0.10 to 19 m.
The system, which received the bauma Innovation Award 2022 in the Machine Technology category last October, is equipped with the latest high-technology that results in a significant reduction in construction times for longer tunnel sections.
Dr-Ing E h Martin Herrenknecht, Founder and CEO of Herrenknecht, comments: “Continuous tunnelling is the next significant innovation step in mechanised tunnelling. New underground traffic routes have to be built ever faster. Continuous tunnelling gives clients and contractors a decisive time advantage that ultimately benefits the entire project and all partners involved. Railroad, metro and road tunnels can be built and put into operation significantly faster.”
Up to now mechanised tunnelling with shield machines in soft ground has been a stop-and-go sequential process. Each excavation stroke is followed by the ring building sequence, so that the excavation has to pause and the subsequent driving cycle be only started when the next segmental ring has been completely installed, which results in loss of time. In contrast, a continuous tunnelling process in which the machine can continue excavation while the lining rings are being installed can contribute to considerable savings in construction time.
“In continuous tunnelling, the thrust cylinders that push the machine forward during advance take over a share of the force of those cylinders that are retracted for ring building,” explains a spokesman for the company. “To ensure that the machine reliably maintains on course under these conditions, the centre of thrust resulting from the combined driving forces of the applied thrust cylinders must remain unchanged in its position. At the heart of continuous tunnelling is, therefore, a powerful computer system and process-specific software programs that can precisely calculate the necessary pressures in the thrust cylinders. It ensures that the machine operator can reliably control the tunnel boring machine along the specified alignment as before.
He continues: “In continuous advance, the machine operator no longer controls the pressures in the thrust cylinders manually using rotary controls (potentiometers) on the control panel. For this purpose, Herrenknecht has newly developed the Center of Thrust (CoT) system, which helps the shield operator to precisely control the machine.The corresponding control of the thrust cylinders is handled by the algorithms in the computer system. Compared to manual control by potentiometers, the CoT offers the prospect of maintaining the specified alignment more efficiently and effectively.”
With continuous tunnelling, an increase in total tunnelling performance of up to a factor of 1.6 can be achieved compared to the previous discontinuous method. This can lead to a significant reduction in construction time for long tunnels. The unique feature of Herrenknecht’s solution is that continuous tunnelling can be used on all machine types in soft ground.
The continuous advance method is being applied for the first time by Bouygues Travaux Publics in the major High Speed 2 project (Chiltern tunnel, 2x16 km) – a new rail link between London and Birmingham, UK.