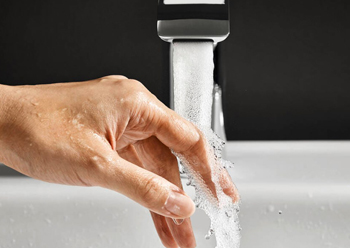
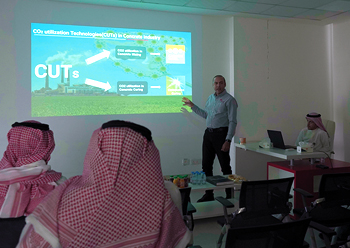
AlKifah Ready-Mix & Blocks (KRB), a leading Saudi Arabian readymix and blocks provider, recently hosted a presentation on its green products, highlighting how its innovative technologies and commitment to research and development are helping to lead the way towards making concrete a more sustainable material.
The presentation, which was attended by top engineers from some of the leading Saudi authorities and companies, underlined KRB’s role as a pioneer in the manufacture of environment-friendly concrete. The audience included senior officials from the Ministry of Energy, Aramco and Saudi Standards Metrology and Quality Organization (SASO). The event was held in late July at the company’s state-of-the-art R&D centre in Al Ahsa.
Ahmad Taha, KRB’s Head of Technical and R&D Division who conducted the presentation, began by discussing the importance of sustainability in the construction industry. He pointed out that cement, a key ingredient in concrete, is responsible for around seven per cent of the world’s CO2 emissions. This makes the construction industry one of the largest contributors to climate change.
“The challenge facing the construction industry is to transform itself from being carbon positive to being carbon neutral,” he said.
To reduce the carbon footprint of concrete production, cement must be replaced with pozzolans, alternative fuels should be used, and CO2 utilisation technologies (CUTS) must be adopted in concrete mixing and curing, Taha pointed out.
KRB’s green concrete solution, ConGreen, is made with local raw materials incorporating carbon dioxide in the mixing process, utilising CarbonCure technology, and natural pozzolans to reduce cement content.
“CarbonCure is produced using technologies licensed from the Canadian company CarbonCure Technologies. The technology involves injecting carbon dioxide into readymix where it converts to a mineral (limestone), improving compressive strength. This allows optimising mix designs, safely reducing cement content by up to five per cent and lowering the carbon footprint of concrete without impacting its quality or performance,” he explained.
The carbon dioxide is captured and distributed by industrial gas suppliers to concrete plants, where it is stored in pressurised tanks. The CarbonCure proprietary equipment, installed in existing concrete plants, injects the precise dosage of CO2 into the mix, where it mineralises.
Using this technology, some 15 to 20 kg of CO2 emissions per cu m are reduced – from the CO2 that is mineralised and emissions avoided through reducing cement content.
KRB has conducted field tests to check the compressive strength (ASTM C39), concrete slump (ASTM C143), air content (ASTM C231) and durability of concrete using optimised mixes. As per the result, these optimised mixes had same or better strength compared to standard mixes and there was no significant impact on concrete slump, air content and durability, Taha stated.
KRB also pointed out that it is the first readymix producer in Saudi Arabia to introduce portable volumetric batch plants, in conjunction with Aramco, to efficiently supply fresh concrete to clients in remote sites.
In line with its focus on sustainability, the company produces two types of natural pozzolan materials that comply with ASTM C618 Class N – Kifacrete-N and Kifacrete-S.
“Pozzolan can reduce the cement content by up to 30 per cent and replace other cementitious materials available in the market, such as fly ash and ground granulated blast furnace slag (GGBFS),” he said.
Taha concluded his presentation by highlighting KRB’s commitment to sustainability. He said KRB is the only supplier of concrete with a verified carbon credit policy in Saudi Arabia, and is focused on reducing its carbon emissions and supporting the development of a more sustainable construction industry.
Major Readymix Provider
KRB has come a long way since its humble beginnings as a single block factory in 1977. Today, the company is the second largest readymix and blocks provider in Saudi Arabia, with more than 27 branches, dedicated site plants, and a workforce of over 1,000.
KRB’s vertically integrated production set-up gives it a competitive edge. The company has its own aggregate crushers, admixture production, and logistics facilities. This allows it to control the quality of its products and deliver them on time and on budget.
KRB’s commitment to sustainability has seen it introduce ConGreen, which has a very low carbon footprint. It also utilises its own aggregate from its crushers in Somman and Hail, which reduces the environmental impact of its operations.
The company, which has a production capacity of 2 million cu m of readymix concrete, has more than 40 batching plants and over 400-strong movable fleet. It also operates the largest state-of-the-art R&D centre in Al Ahsa.
KRB provides different types of concrete as per client requirements and specifications, the construction methodology and area of application. These include normal strength, reinforced, prestressed, lightweight, high-strength, high-performance, self-compacting and stamped concrete.
In addition to readymix concrete, KRB also produces more than 150,000 blocks per day at two automated block factories in Hasa and Hail, and a manual block factory in Dammam. The variety of blocks it offers comprises insulated, cement, curbstone, interlock, and Hordi blocks. The company’s product mix also includes Blogreen, a new generation of green blocks with a low CO2 footprint.
KRB is a member of Kifah Construction Solutions, which also includes Kifah Contracting, KiCE Construction Equipment, AlKifah Precast Company (KPC), and KILO, which offers logistic solutions.